WE
ARE
RESONAC
GRAPHITE.
Resonac’s Graphite Business Unit is the leading producer and supplier of graphite electrodes worldwide. Our product serves as a vital component in the electric arc furnace (EAF) steel-making process.
We take pride in fostering sustainable societal progress by supporting the efficient use of recycled steel.
With a legacy spanning over a century, Resonac Graphite is dedicated to crafting high-quality electrodes tailored to EAF, ladle furnaces, and non-ferrous smelting applications.
Resonac Graphite is a subsidiary of Resonac Holdings Corporation, a collection of chemical companies producing petrochemicals, chemicals, inorganics, aluminum, and electronics.
With a workforce of approximately 26,000 employees worldwide, we continue to innovate and deliver specialized products that meet the evolving needs of our global clientele.
Welcome to the Resonac Graphite Business Unit, where we embrace the transformative power of people and their ability to reshape the world. As a global leader in graphite electrode production, our dedication to sustainability goes beyond rhetoric – it's a core element of who we are.
In the ever-evolving landscape of decarbonization, the Resonac Graphite Business Unit approaches challenges directly. We are dedicated to developing innovative solutions that align our organization with a more sustainable future.
Our Core Values
Agile &
Flexible
Passionate &
Results-Driven
Solid Vision &
Solid Integrity
Open Minds &
Open Connections
As an essential member of the multinational Resonac Group, we operate manufacturing facilities in Asia, Europe, and North America.
Resonac Graphite is committed to societal change through the transformative power of chemistry. We actively engage with internal and external partners to nurture a culture of co-creation that is deeply ingrained in our DNA.
Join us on a journey of innovation, sustainability, and partnership, shaping a future that echoes the core values of Resonac!
world wide
employees
Resonac Graphite
every second our
products melt
tons of steel
world wide
production sites
Production
plants
resonac
graphite
world wide.
Resonac’s graphite electrodes are produced globally at six locations, and delivered to customers around the world. Our regional presence enables short lead times and reliable supply chains - ensuring that our customers’ needs are met quickly and efficiently.
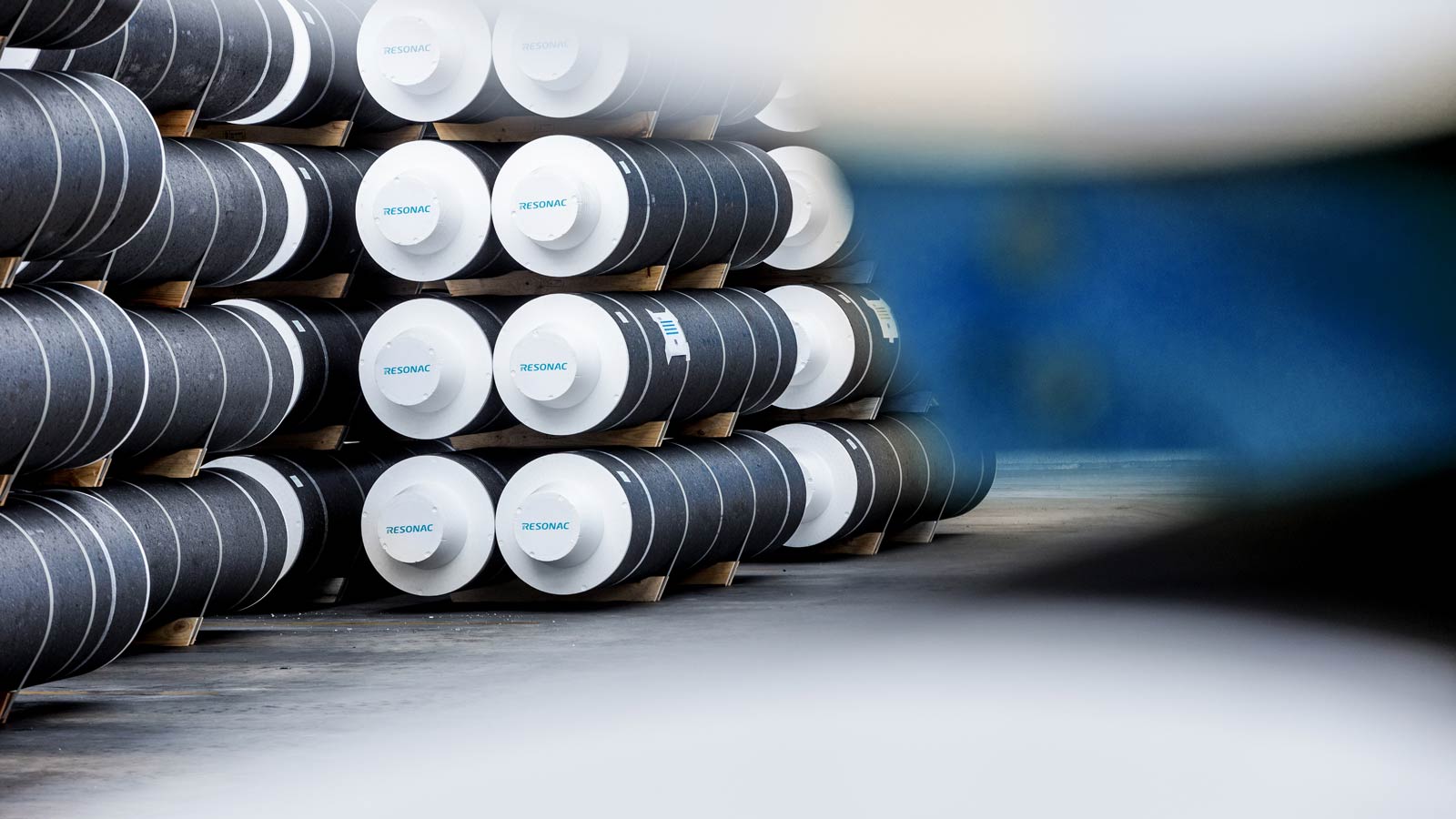
The
Power
of
Technology.

One of our core convictions is that we sell value, not volume. By that we mean, our business surpasses the customer-to-supplier transaction. We take a great interest in understanding what value means to our customers.
Innovation, such as our ΩMEGA electrode, was developed based on the unmet needs of our customers.
ΩMEGA is a ladle furnace electrode that is manufactured in Europe using 100% renewable electricity. The conception and successful development of the ΩMEGA is just one example of how we partner with our customers.
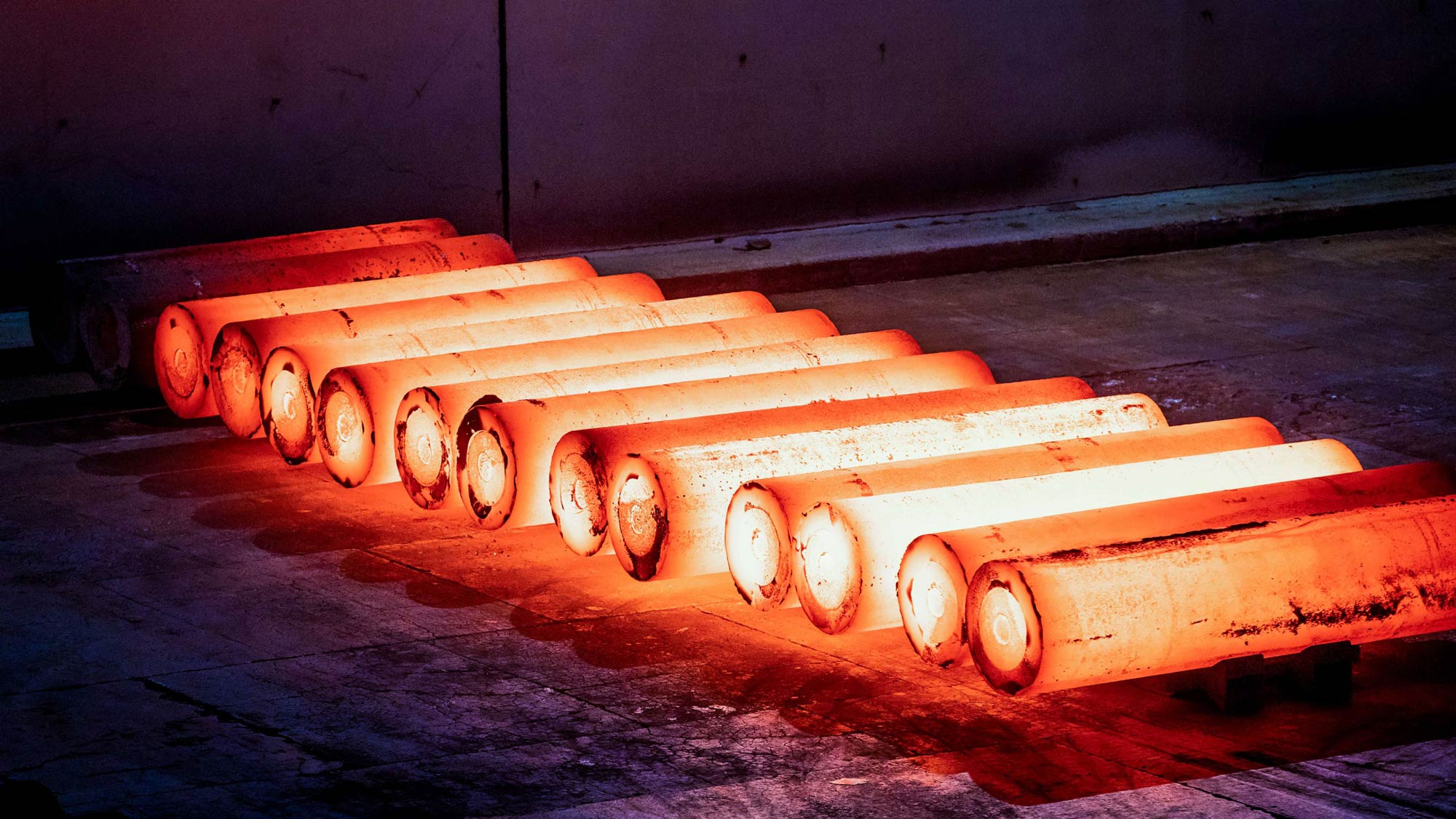
Graphite
Electrodes.
Graphite
Electrodes.
Standard Diameter:
350 – 800 mm / 14 – 32 inches
Standard Length:
1,500 – 3,600 mm / 60 – 142 inches
Typical Weight:
0.3 – 3.2 tons
Typical consumption rate:
1 – 2 kg graphite per ton of liquid steel
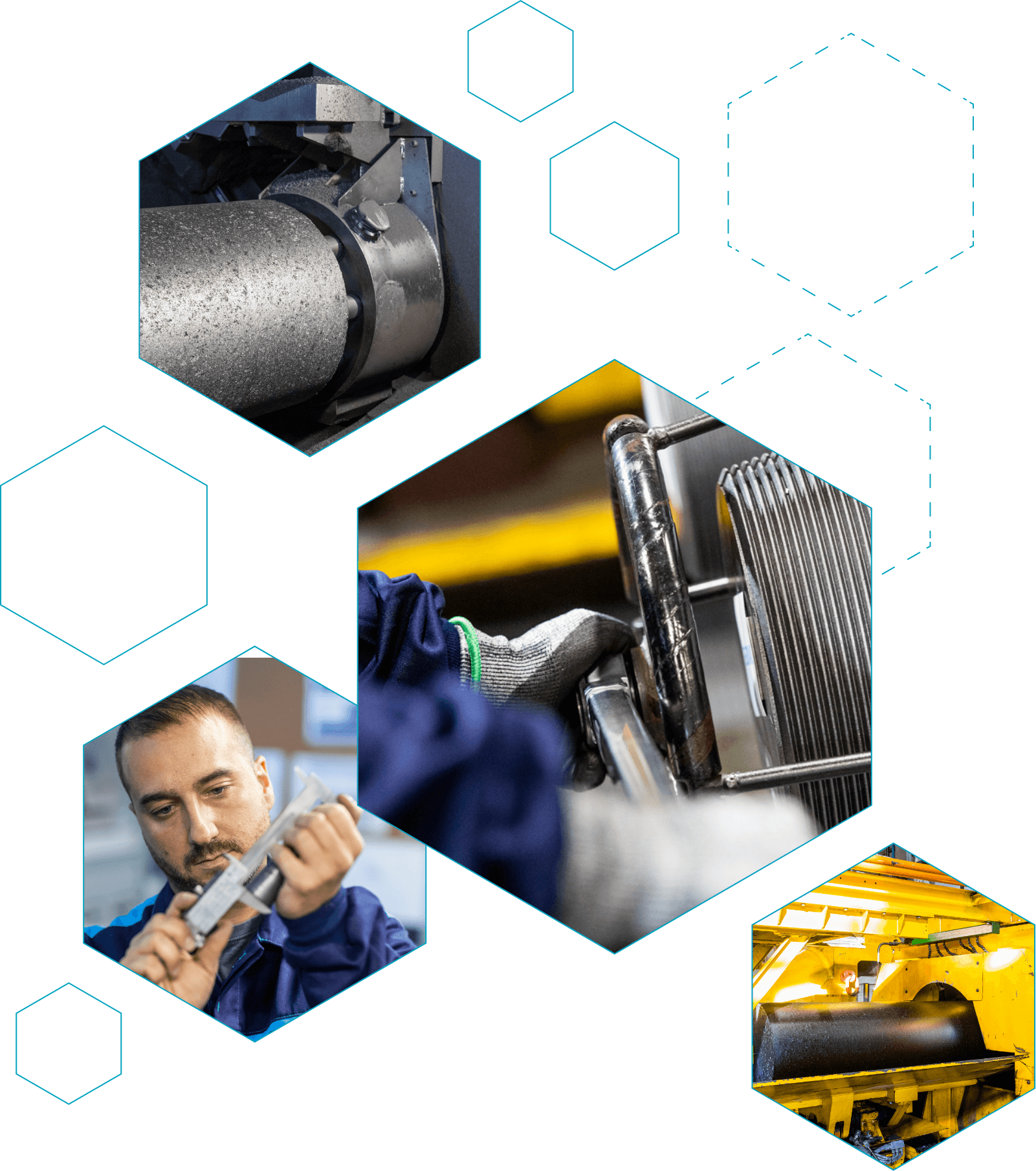
Graphite
Electrodes.
Graphite electrodes are primarily used in the production and recycling of steel.
During the process, steel scrap is melted in a large crucible (furnace) by an electric arc. This is the genesis of the name “Electric Arc Furnace” (EAF). The arc is a channel of ionized air through which electric current passes from the electrode into the steel scrap. A similar phenomenon occurs during a thunderstorm with the rapid discharge of electricity that we know as lightning.
In the steel mill, the furnace is loaded with steel scrap. Then, one column (direct current furnace) or three columns (alternating current furnace) consisting of multiple graphite electrodes screwed on top of each other, is introduced and the arc is ignited. The arc is maintained for a few minutes so that a generated temperature of around 3500 degrees Celsius can rapidly melt the scrap in the furnace. The molten steel is then poured off for further processing. This procedure is known as tapping. Typical cycle times, i.e., the time between two taps, are between 45 and 90 minutes.
Approximately one-third of the world’s steel is produced via EAF, making it the largest recycling process globally. Compared to steel made using a basic oxygen furnace (BOF), the EAF process bypasses around 80% of direct CO2 emissions per ton of steel.
But why do electrodes have to be made of graphite? If the electrodes that conduct the current were made of metal, like many electrical devices, it would simply melt like the scrap does. Other materials, like ceramic, can withstand the heat, but are not good conductors of electricity. It’s essential to have a material that can conduct an electric current without melting when exposed to elevated temperatures. Graphite is an excellent solution.
Despite its extraordinary properties, the graphite electrode is consumed during the melting process – primarily through oxidation. As the electrode wears down, it must be replaced by a new one. The quality of an electrode is typically measured by the rate of consumption per liquid ton of steel melted. The lower the consumption rate, the better for electric steelmakers.
Steel 
industry
with
Resonac.
70%
of CO2 Emissions
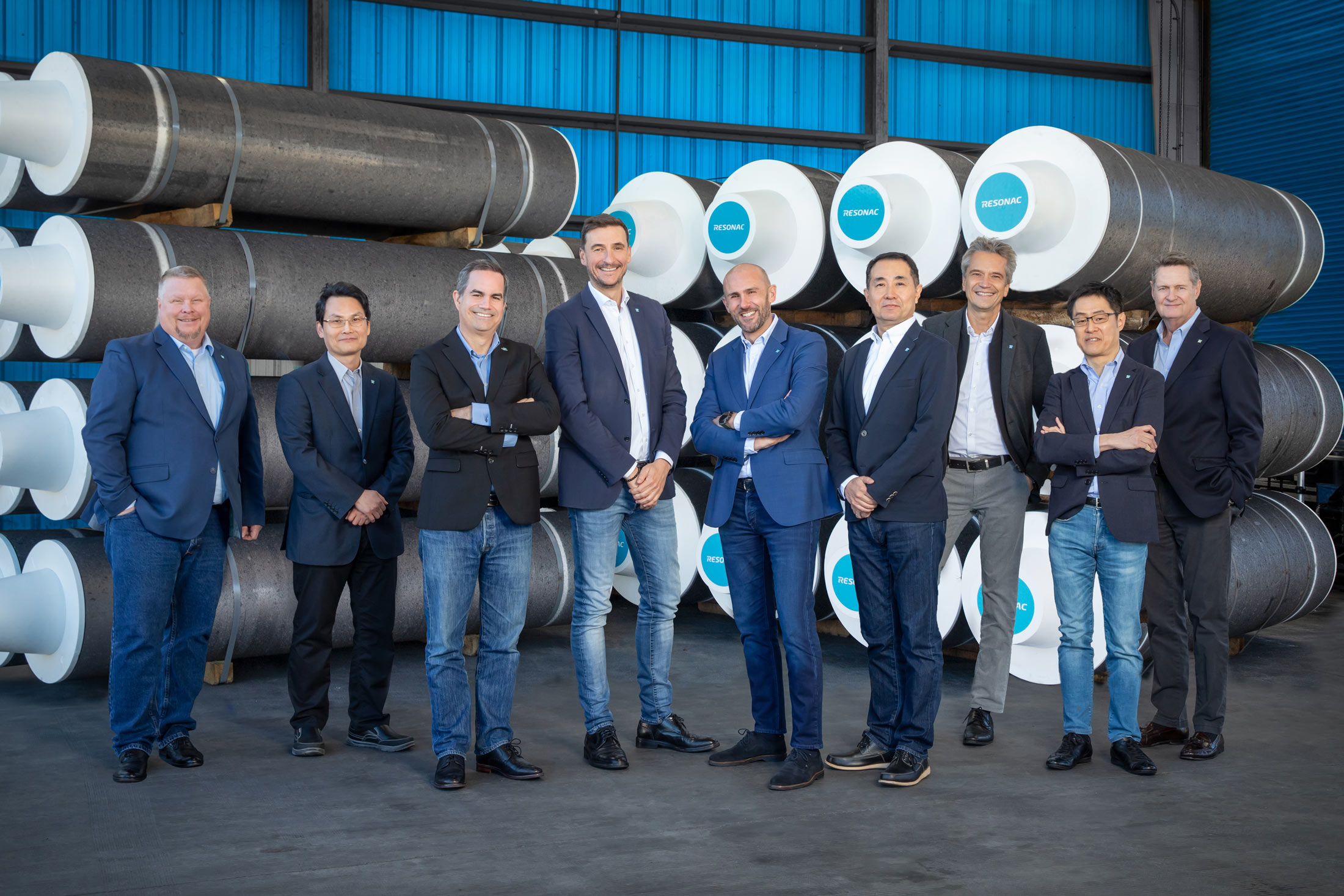
Tim Saxon Chief Marketing Officer, Giwon Park Chief Human Resources Officer, Daniel Duenas President & CEO Americas; Chief Manufacturing & Engineering Officer, Cesar Castineira President & CEO Graphite Business Unit; Chief Operating Officer, David Germade President & CEO EMEA, Tomoki Katayama President & CEO Asia, Dr. Michael Kuschnick General Counsel, Taku Tanaka Chief Financial Officer, Carl Kolts Chief Strategy Officer
Our
Management
World
Wide.
Resonac Graphite is led by an international team that continuously drives us toward sustainable resilience by leveraging global synergies and functional standards while implementing strategies that take into account regional particularities:
We encourage, inspire, and motivate our team to contribute and innovate so that they can grow and develop as we empower them to shape the future of not only our company but of society as well.
We challenge assumptions, take risks and explore new ways of doing things and new opportunities to learn, and are enthusiastic and model high ethical behavior to our colleagues, customers, and partners.
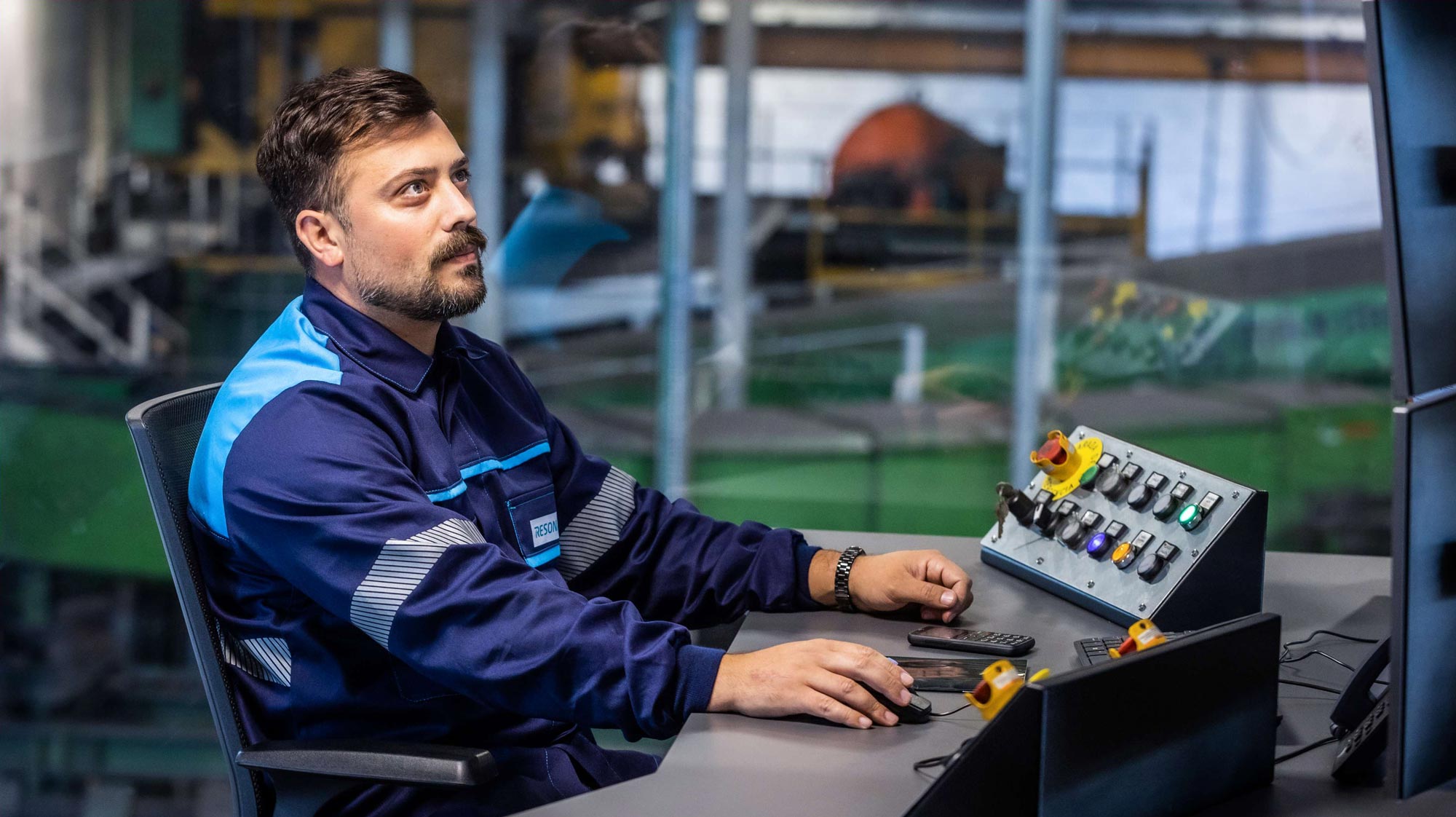
Our Way
to
Excellence.
We are a growing company aiming to become a global top-level functional chemicals manufacturer which can compete on the world stage. To achieve this goal, we are looking for passionate and results-driven people who want to participate and contribute to our success.
INTERESTED IN JOINING RESONAC?
We believe in diversity and that a diverse team makes our company more successful. Therefore, we are looking forward to your application, without regard to nationality, race, gender, age, disabilities, religion, other backgrounds, sexual orientation, skills, experiences, or worldview.
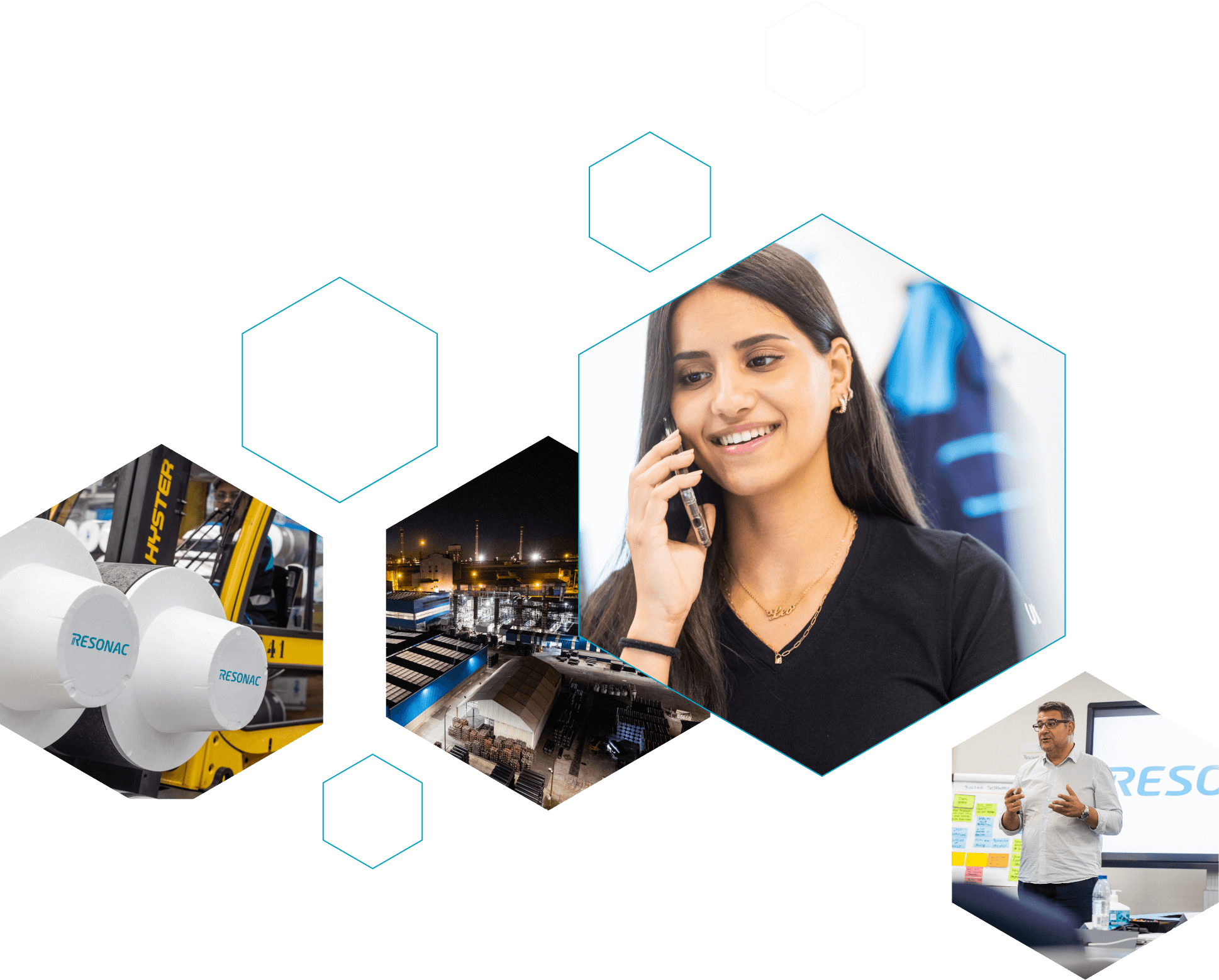
We believe the world is rapidly moving away from competition between individual companies and toward competition between end-to-end supply chains. In preparation, we are developing strategic partnerships with select customers and suppliers to give us a competitive advantage. These relationships are the pillars of our goal to achieve a profitable, resilient, and sustainable operation.
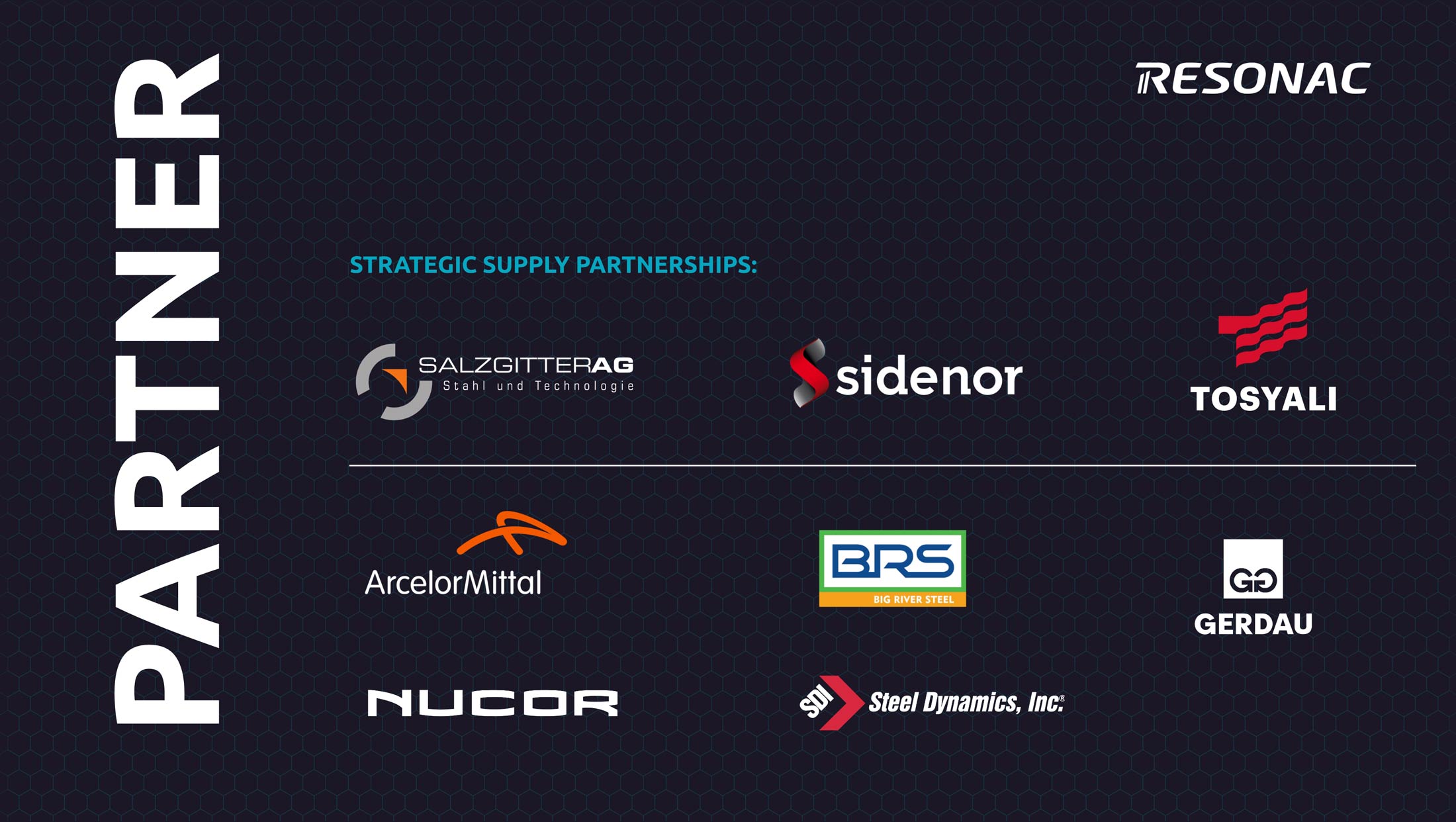
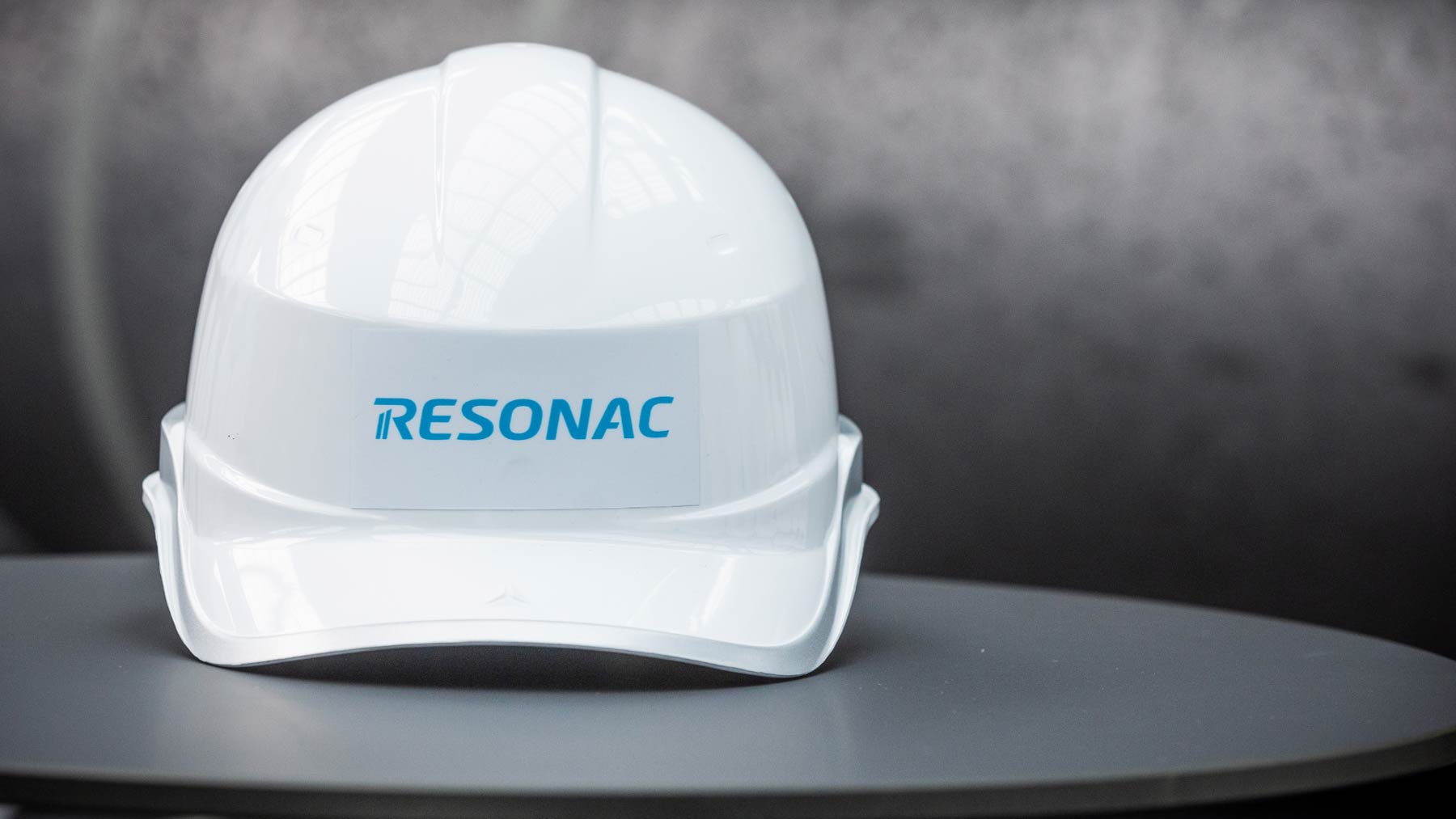