Overview
Products.
We, Resonac’s Graphite Division, are the world’s main producer and supplier of Graphite Electrodes. Our product is a crucial part in the world’s largest recycling process:
The recycling of steel in Electric Arc Furnaces.
We are proud to say: We enable a sustainable advancement of society by helping to recycle steel in an efficient and environmentally friendly way.
Resonac Graphite has been making high-quality electrodes for use in electric arc furnaces (EAF), ladle furnaces (LF), and non-ferrous smelting applications with over 100 years of experience and delivering to steel makers worldwide.
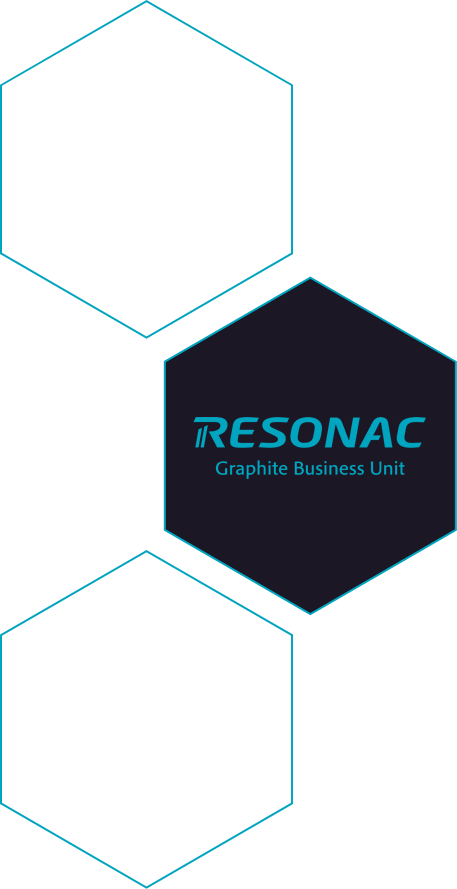
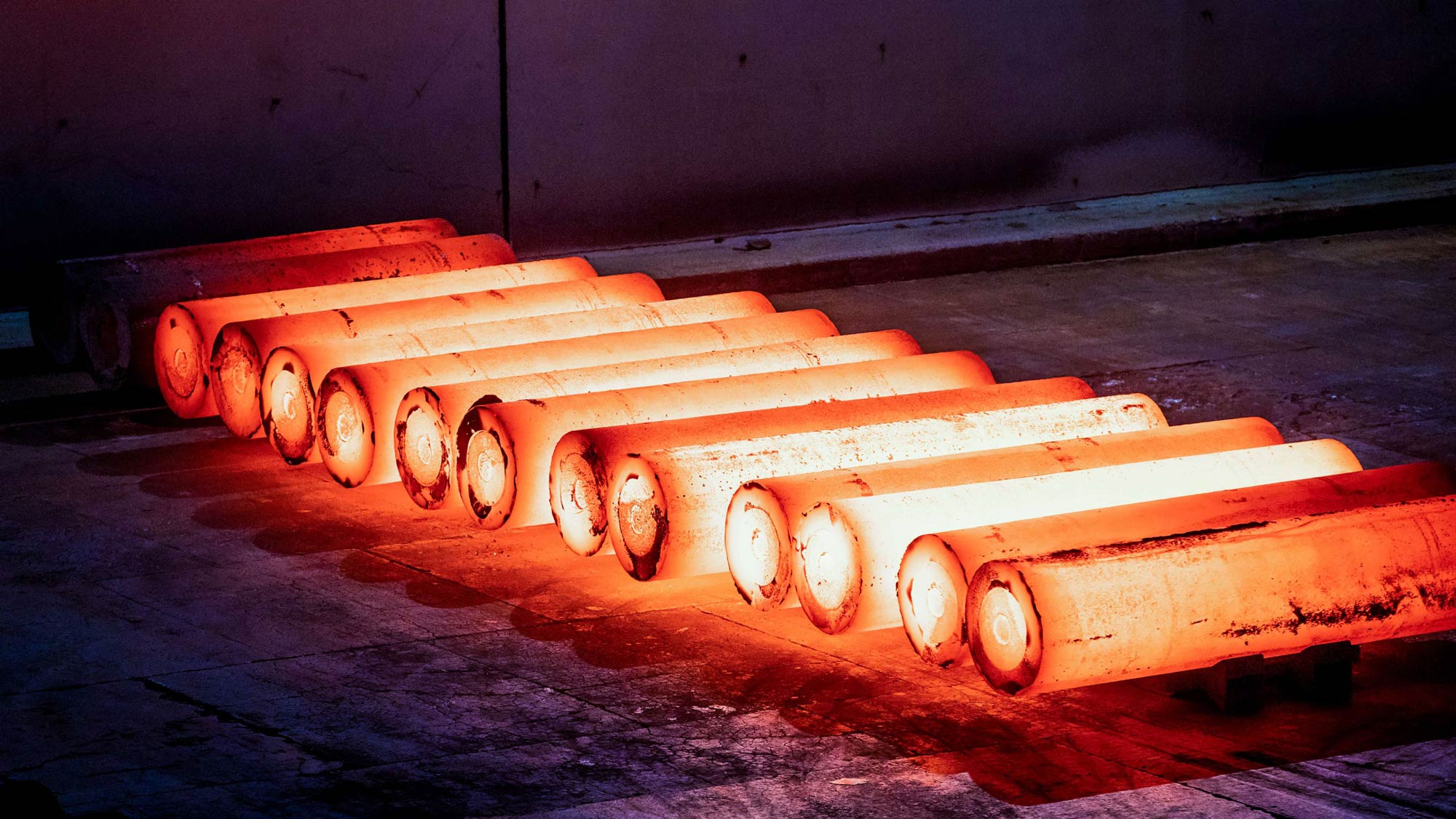
Graphite
Electrodes.
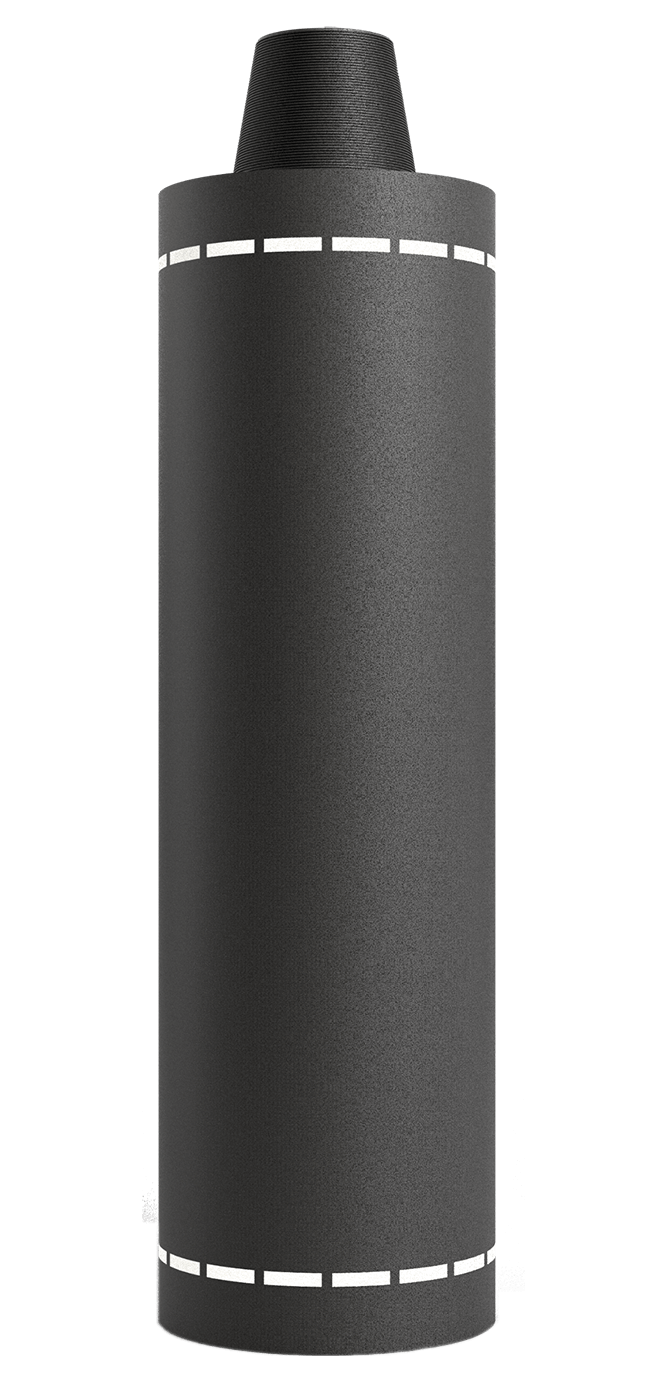
Graphite electrodes are primarily used in the production and recycling of steel.
During the process, steel scrap is melted in a large crucible (furnace) by an electric arc. This is the genesis of the name “Electric Arc Furnace” (EAF). The arc is a channel of ionized air through which electric current passes from the electrode into the steel scrap. A similar phenomenon occurs during a thunderstorm with the rapid discharge of electricity that we know as lightning.
In the steel mill, the furnace is loaded with steel scrap. Then, one column (direct current furnace) or three columns (alternating current furnace) consisting of multiple graphite electrodes screwed on top of each other, is introduced and the arc is ignited. The arc is maintained for a few minutes so that a generated temperature of around 3500 degrees Celsius can rapidly melt the scrap in the furnace. The molten steel is then poured off for further processing. This procedure is known as tapping. Typical cycle times, i.e., the time between two taps, are between 45 and 90 minutes.
Approximately one-third of the world’s steel is produced via EAF, making it the largest recycling process globally. Compared to steel made using a basic oxygen furnace (BOF), the EAF process bypasses around 80% of direct CO2 emissions per ton of steel.
But why do electrodes have to be made of graphite? If the electrodes that conduct the current were made of metal, like many electrical devices, it would simply melt like the scrap does. Other materials, like ceramic, can withstand the heat, but are not good conductors of electricity. It’s essential to have a material that can conduct an electric current without melting when exposed to elevated temperatures. Graphite is an excellent solution.
Despite its extraordinary properties, the graphite electrode is consumed during the melting process – primarily through oxidation. As the electrode wears down, it must be replaced by a new one. The quality of an electrode is typically measured by the rate of consumption per liquid ton of steel melted. The lower the consumption rate, the better for electric steelmakers.
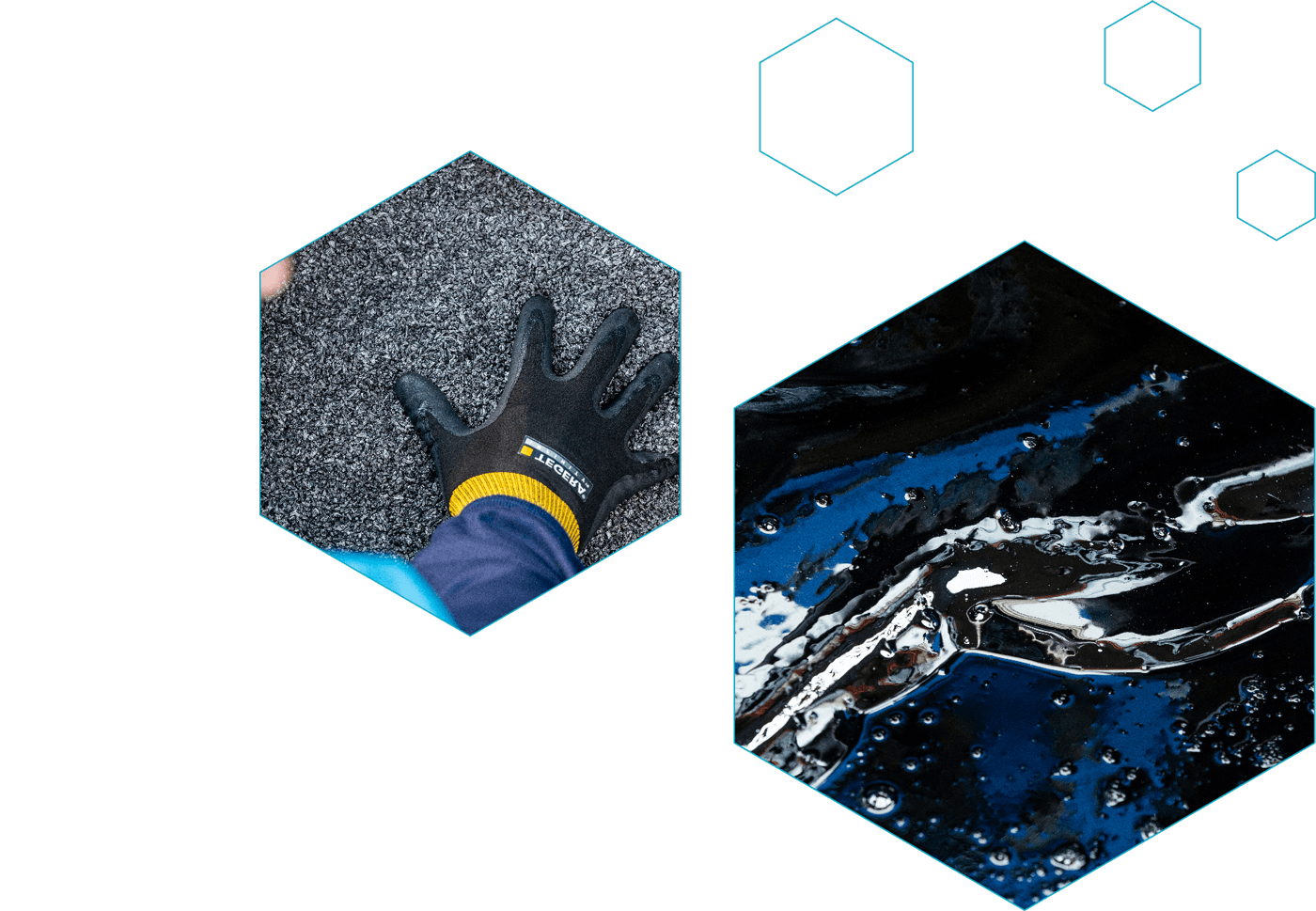
Graphite
Electrodes.
Graphite
Electrodes.
Standard Diameter:
350 – 800 mm / 14 – 32 inches
Standard Length:
1,500 – 3,600 mm / 60 – 142 inches
Typical Weight:
0.3 – 3.2 tons
Typical consumption rate:
1 – 2 kg graphite per ton of liquid steel
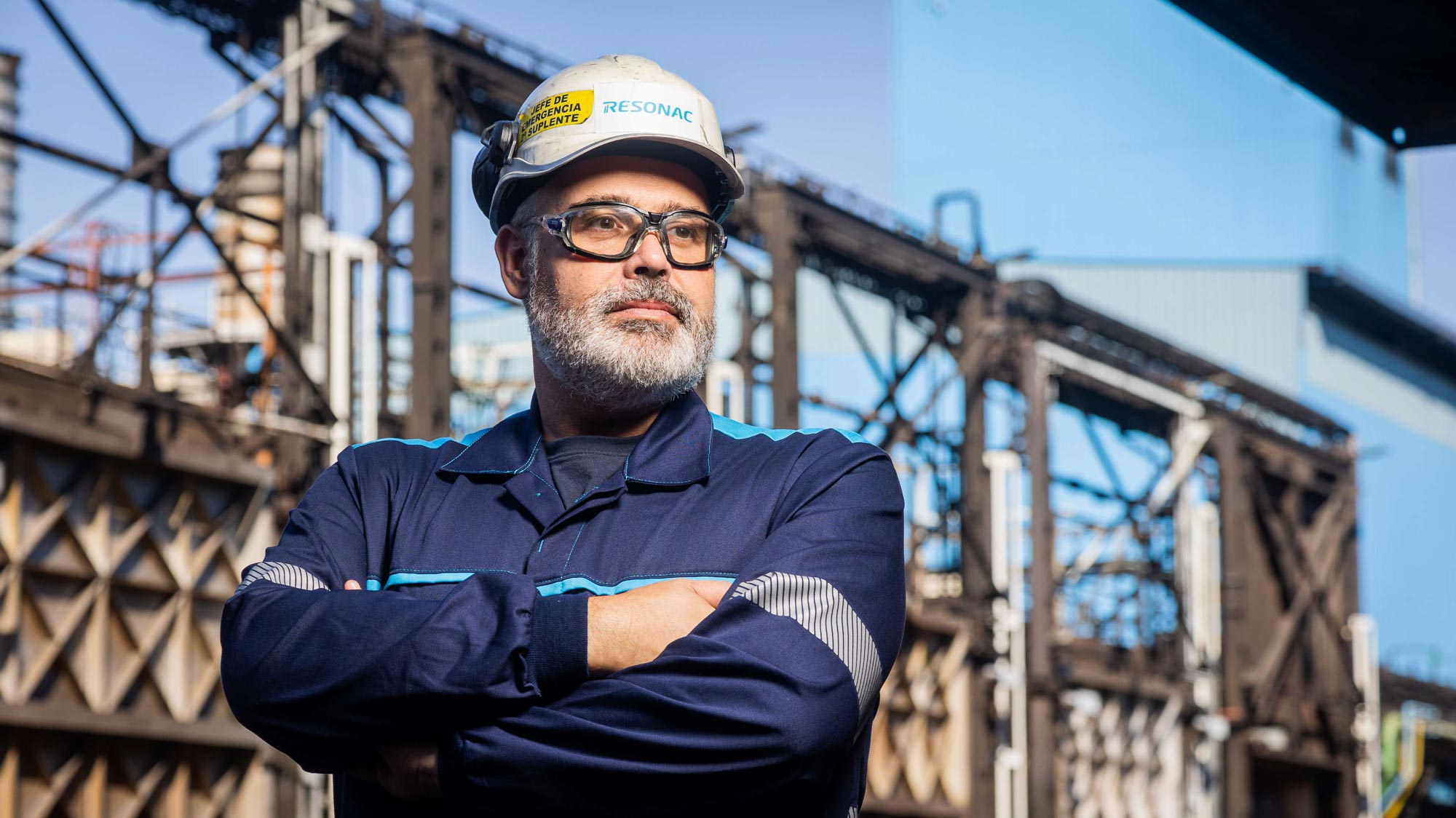
Production
of
Graphite
Electrodes.
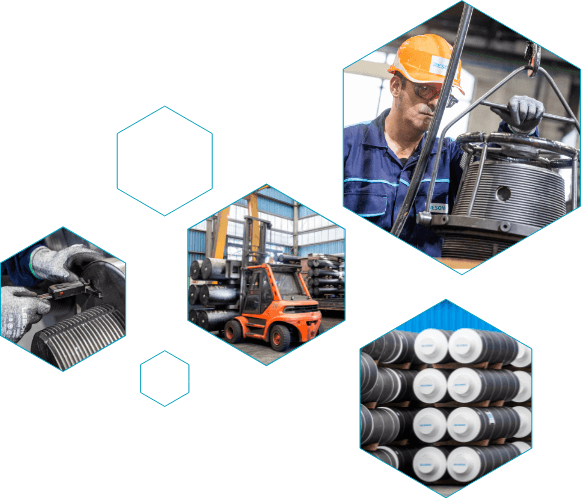
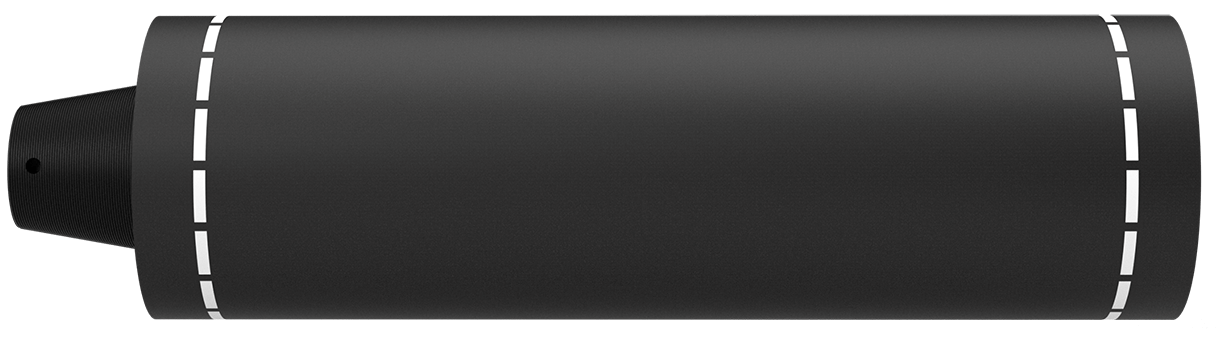
Connecting
Pin.
With over 85 years of experience manufacturing graphite electrodes and connecting pins, our plant in Omachi, Japan is capable of producing the highest quality products to meet particular EAF requirements.
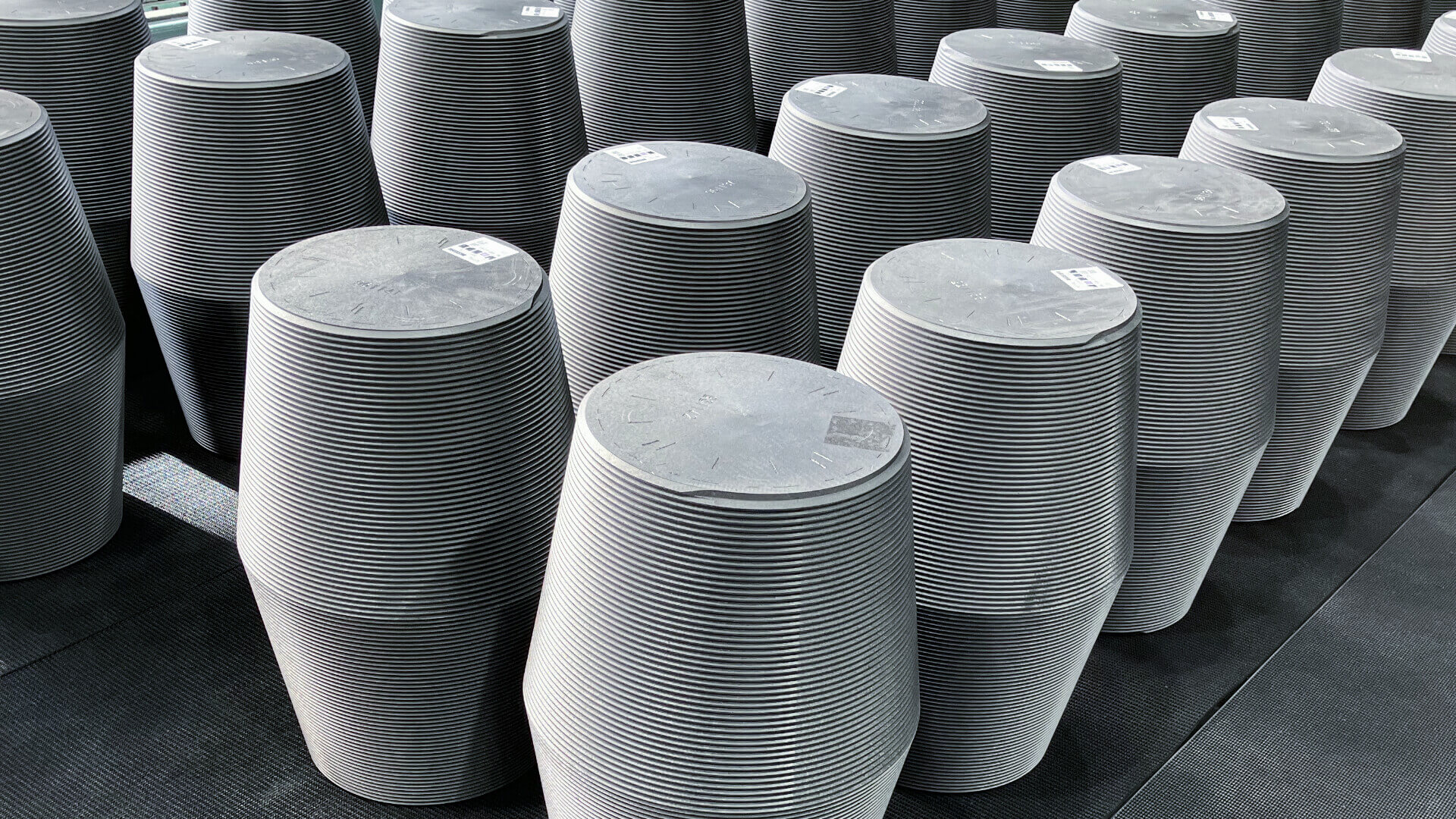
Product
Performance
Development.
At Resonac Graphite Business Unit, our commitment goes beyond graphite electrode sales. Our global network of PPD (product, performance, and development) experts is dedicated to addressing a wide array of topics related to our products and their applications. Whether it is providing training on electrode handling, conducting performance evaluations and analyses, or engineering tailored solutions for specific needs, our PPD experts ensure that our clients maximize the benefits of our products.
With a wealth of experience within our team, we bring innovative applications of product and process knowledge. We actively listen to our clients, considering their ideas as opportunities for co-creation. Having supplied graphite electrodes to over 2,000 electric arc furnaces worldwide, we possess a profound understanding of the diverse applications of EAF steelmaking. Our PPD experts are eager to partner with our customers' technical and operational teams, offering a full range of support to meet their needs.
Choose to partner with Resonac Graphite for a comprehensive and collaborative approach to optimize your steelmaking processes.
We can provide solutions tailored to your specific situation and furnace.
Our services include:
- Product monitoring
- Performance analysis
- Inventory control
- Inspection of accessories
- Monitoring of electric arc furnaces
- Tailor-made data analysis
- Consumption model to check theoretical and real consumption data
- Calculation of productivity
- Recommendations for EAF design and operational questions
- Furnace start-up assistance
- Electrical energy modeling
- Regulation tuning
- Hydraulics
- Power (melting) profiles
- Workshops on customer request
- Customer cooperation
- Tools and methodologies