ESG FOR TRANSFORMING SOCIETY THROUGH THE POWER OF CHEMISTRY
Our sustainability brand, Sparking Truth, is a call to all steel industry stakeholders to unite towards a shared vision. A vision that protects our well-being, preserves nature, and fosters human development – all within a partnership rooted in transparency and shared principles of governance.
ARE YOU IN?
Now is the time to act. This is a collective effort - we cannot achieve this alone. Let’s transform society so that every action sparks positive change.
WE ARE...
We
are
environmental.
We are committed to reducing our carbon footprint and mitigating the impact of our operations on the environment. Among our most challenging goals we have set a target for carbon neutrality by 2050 and have developed a carbon reduction plan to achieve this goal, focused on the use of green electricity, emissions reduction and increased efficiency. In addition, we are constantly exploring new ways to reduce waste through the adoption of more efficient production processes.
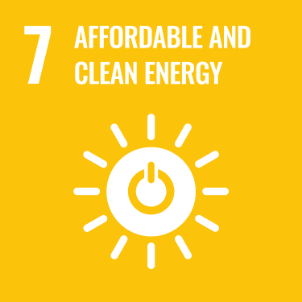
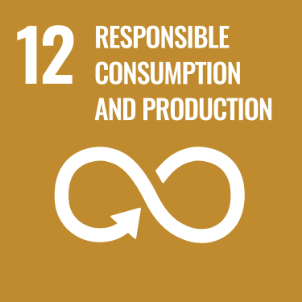
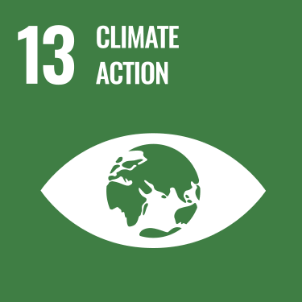
Green
Electricity.
We are committed to reducing our carbon footprint through the increased use of renewable energy.
Since 2022, our plant in Steeg, Austria, has been fully powered by green electricity, making it one of the few in the industry operating at 100% renewable energy.
In addition, as of 2024, our plant in A Coruña, Spain, secured 40% of its electricity consumption through a long-term Power Purchase Agreement (PPA) for renewable energy.
In 2023, our plant in Malaysia installed 1 MWp of solar photovoltaic panels, generating 1.25 GWh annually and reducing CO2 emissions by 975 tons, showcasing our commitment to using green electricity.
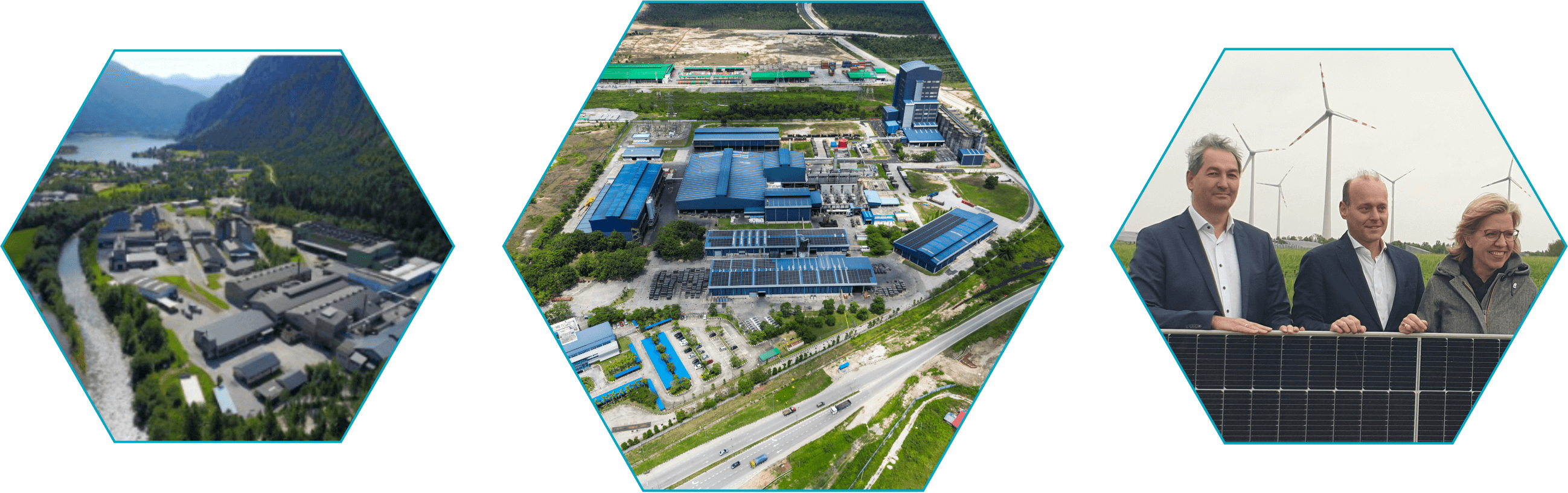
Emissions
Reduction.
Our commitments to the environment are not just words. In addition to the progress we are making to increase the supply of electricity from renewable sources, our plant in A Coruña is working on the implementation of green hydrogen burners in the incinerator of the new baking furnace.
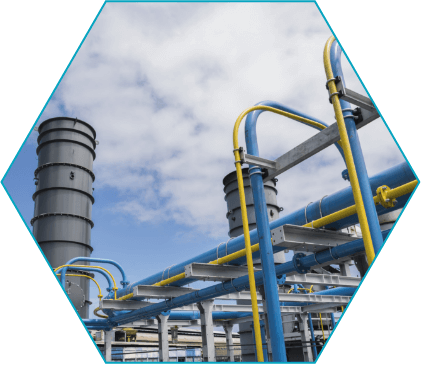
Increased
Efficiency.
An important part of sustainability is the use of existing resources. With this objective in mind, Endesa X has designed a customized system for recovering the heat obtained during the firing phase of the graphite electrodes for the A Coruña factory. Thanks to this project, the Resonac Graphite BU plant in Spain will achieve a 70% reduction in the consumption of gas boilers and a 30% reduction in the electricity consumption of stoves.
Circular
Economy.
We are committed to transitioning towards a circular economy, where resources are reused, recycled, and regenerated. By minimizing waste and maximizing resource efficiency, we aim to create sustainable value throughout our processes. Our initiatives focus on reducing environmental impact, innovating through recycling, and fostering a closed-loop system that supports a sustainable future for all.
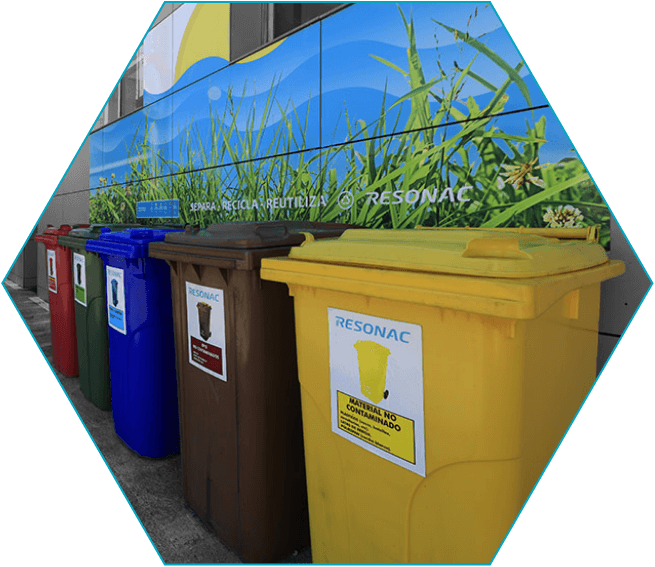
Waste
Management.
We believe that responsible waste management is essential for a sustainable future. As part of this commitment, we have adopted the ISO 14001 framework, a globally recognized standard for effective environmental management systems. To further drive our sustainability goals, we are implementing a Harmonized and Global Waste Management System based on the Global Reporting Initiative (GRI) Standards. This system aims to create a unified waste categorization approach worldwide, enhancing our strategies for waste reduction, recycling, and reuse.
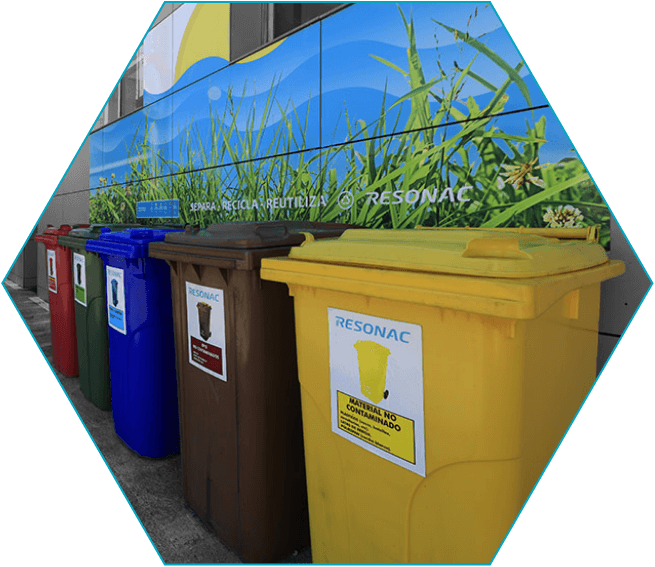
Zero
Paper Programm.
We are advancing our sustainability efforts through the Zero Paper Program, aimed at transforming and optimizing our operations via digitalization. By transitioning to digital processes, we enhance operational efficiency and leverage technology combined with the advanced digital skills of our people. This initiative not only reduces paper waste but also supports the broader goals of digital transformation within our organization.
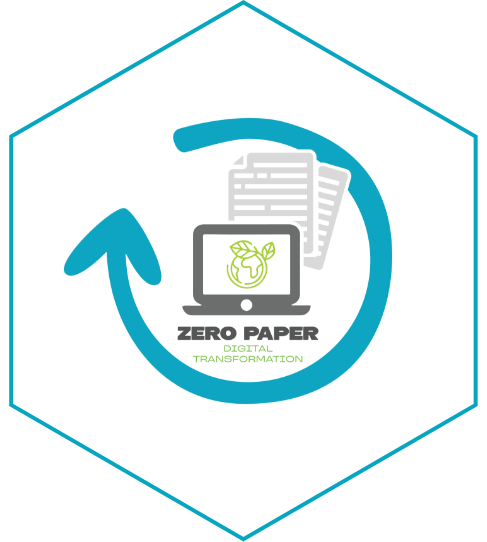
Water
Management.
We recognize that effective water management is vital for sustainability and operational efficiency. In 2023, we implemented an innovative Water Recycling System at our A Coruña plant to enhance the efficiency of our electrode production process through advanced water management technologies.
This system features a cutting-edge Water Temperature Control mechanism that regulates the cooling of electrodes, optimizing the process and improving operational efficiency. By recirculating the water used in production, we have significantly reduced water consumption per ton of product.
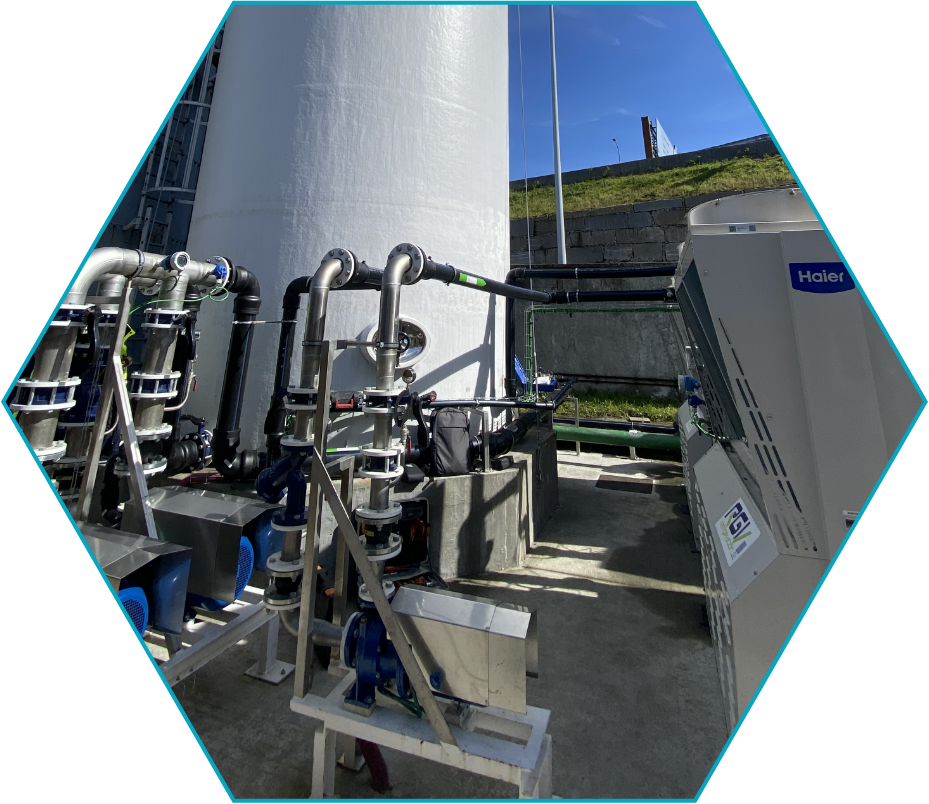
We
are Social.
We prioritize the holistic development of our people, recognizing that their growth and well-being are fundamental to our collective success. We strive to foster an inclusive and supportive work culture that embraces diversity and empowers individuals to reach their full potential. By creating safe and equitable environments, we are committed to building a strong foundation for our employees to thrive and contribute to a sustainable future.
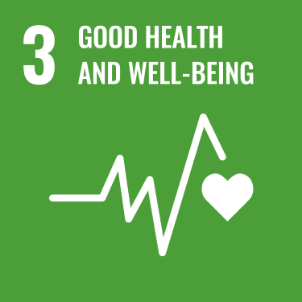
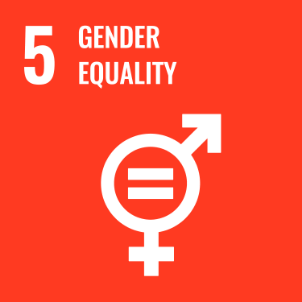
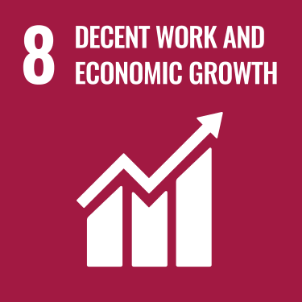
People
We believe in the transformative power of investing in our people. Our commitment to talent development goes beyond the ordinary—it’s about creating an organization where our people are not just employees but valued contributors to our shared success story. We recognize that the heart of our company is its people, and we are dedicated to providing an environment where growth, learning, and innovation flourish.
In our pursuit of excellence, we aim to be more than just a workplace; we strive to be a community where every team member is encouraged to unleash their potential. Our emphasis on talent development is a testament to our vision as a place where our employees can build fulfilling careers. We are driven by the idea that our workplace should be one where we’d be proud and excited to welcome our own loved ones.

Our Way to Excellence (OWEx) is the holistic system by which Resonac Graphite promotes the understanding of end-to-end processes, transformational leadership, cross-functional collaboration, and talent development. OWEx is designed to support regions, functions, and sites on our shared transformation journey towards excellence, thus building the basis for developing talent across the whole organization.

The Employer of Choice Program is a global initiative to make Resonac Graphite the company where our employees and their loved ones want to work.
It is all about creating a positive and inclusive environment, engaging talents and increasing satisfaction in their workplace. With a multitude of projects, the Employer of Choice Program shall strengthen physical and psychological safety and provide opportunities for development in a friendly, performing community with open and transparent communication.
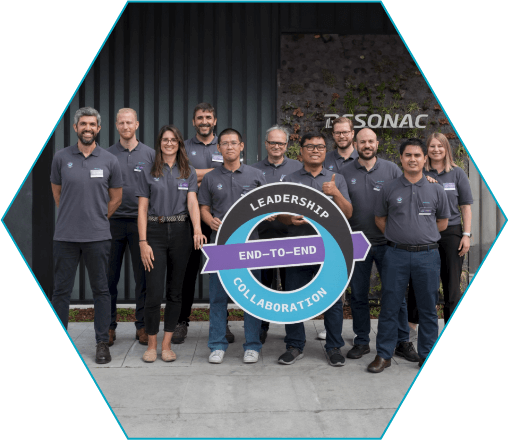
Safety
We are very proud to be part of a company where safety does not compete with production. We work to have a place where we would like our loved ones to work; that is our motto and that is our way of doing things.
For us, the daily work in HSE is oriented in three directions:
- Each of us can be a Safety Leader. Every day we have many opportunities to lead in safety by setting an example with our attitude and performance.
- Safety is an issue for all of us. That’s why Teamwork and Passion for what we do is the only valid route to achieving the highest HSE standards.
- Our Commitment to HSE represents the peace of mind of our families who know that we are cared for at work just as we are cared for at home.
Below you will be able to access some of the initiatives with which we add value to our business:
We believe that effective communication is the foundation of trust in any organization. Under this premise, we launched BAD NEWS FIRST, an initiative aimed at transforming communication and increasing transparency at all levels.
What began as a communication tool has quickly evolved into our working philosophy. BNF has fundamentally changed the way we approach safety in our workplace and our focus on people.
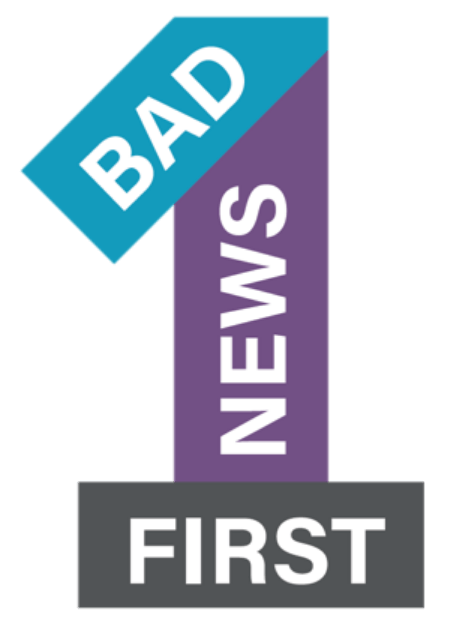
In 2020, a project ended with the goal of bringing all our safety processes to the attention of all the organization. To do so, we knew that the only way to really reach everyone was to make it approachable and congenial.
The guidelines were clear, but the real challenge was to make the employees, who are at the forefront of the company’s production processes, see that safety should be tackled as a priority and made a part of our DNA, the essence of our personal and professional vision.
This is how the Safety Rangers came into being, eight superheroes who represent each of our sites and who are also connected to our approach to Health, Safety and the Environment.
Our mascots, just as our unsung leaders do every day, have a clear mission: to stop Risk, the villain who is on the lookout for the slightest mistake to cause an accident.
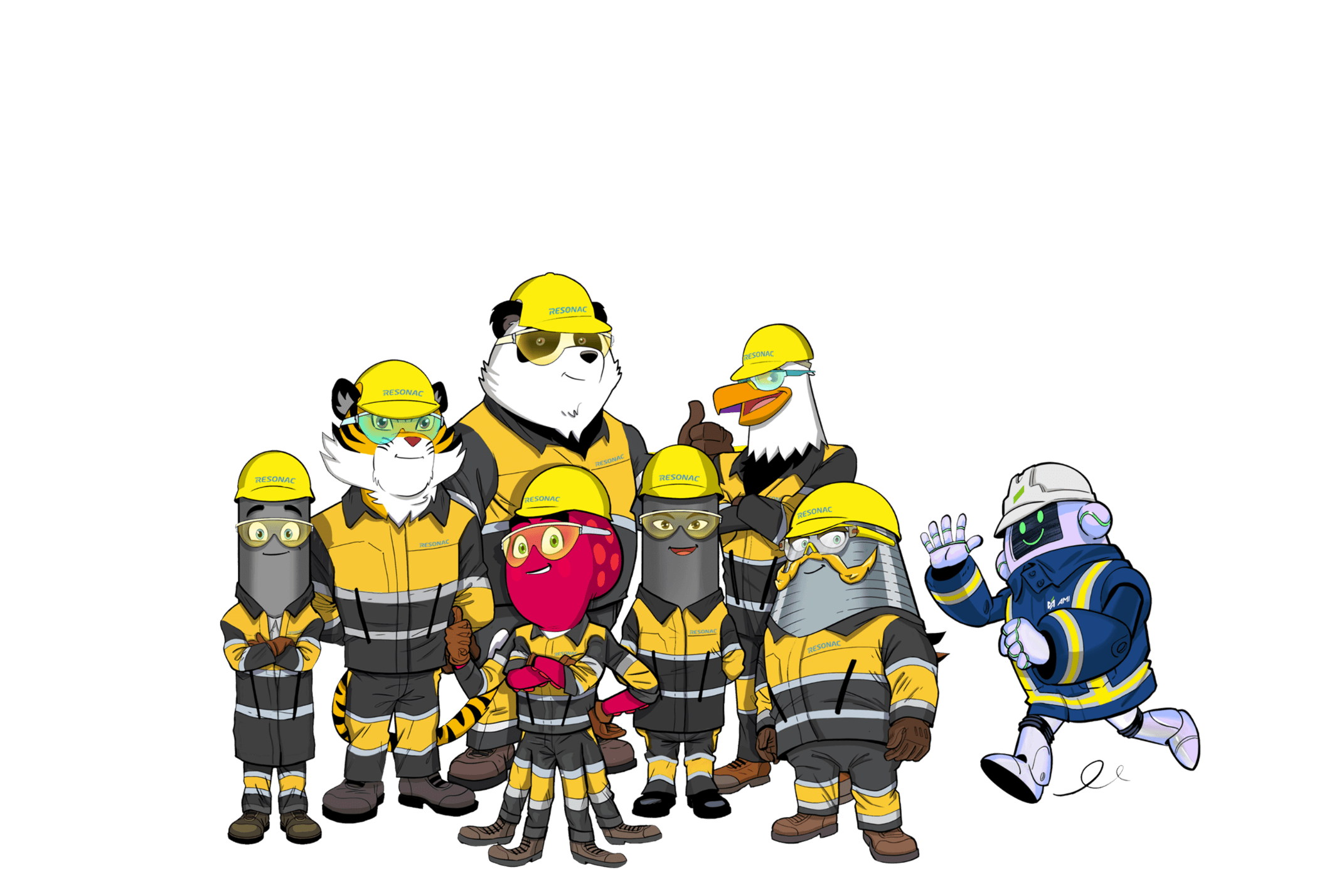
Carboni as energy expert, Mr. Sagger as green guide, An An as veggie vindicator, Safety SAM as fume fighterr, AMITRON - -- - -- ----- ---, Mr. Pin as truth talker, Denkyokukunk as recycle ranger, Electroctopus as water wizard
Making safety expectations explicit is very important to activate the possibility of connecting our employees with a better version of themselves.
Our 10 Safety Action Rules act on the main risks of our business, encouraging positive safety behavior and helping to generate a higher maturity level in our Safety Culture.
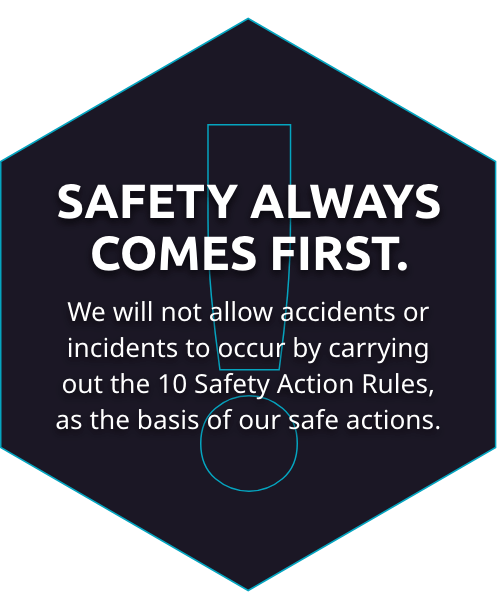
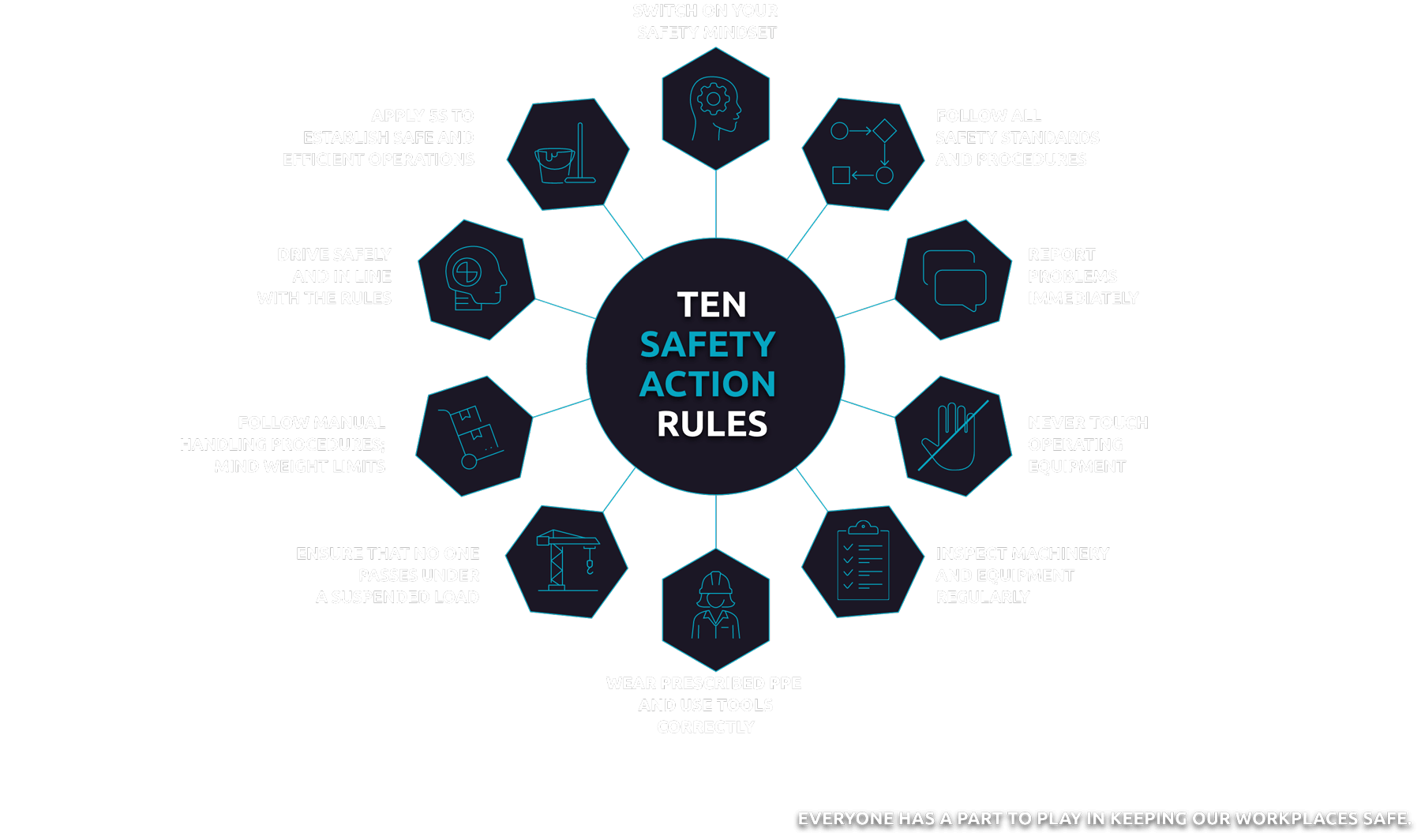
Thinking in safety since the first design concept is drafted, conducting process hazards analysis in early stages (iteratively if needed) and involving designers, HSE department, production and maintenance from the beginning of a project.
This approach helps teams to have a better understanding of the possible risks for facilities and operators. Common risk appetite/awareness generates synergies between team members, who naturally collaborate to create a design that reduces risk of accidents to the minimum levels possible. The real value is that we change the thinking from “this will probably not happen” to “we cannot allow this to happen”
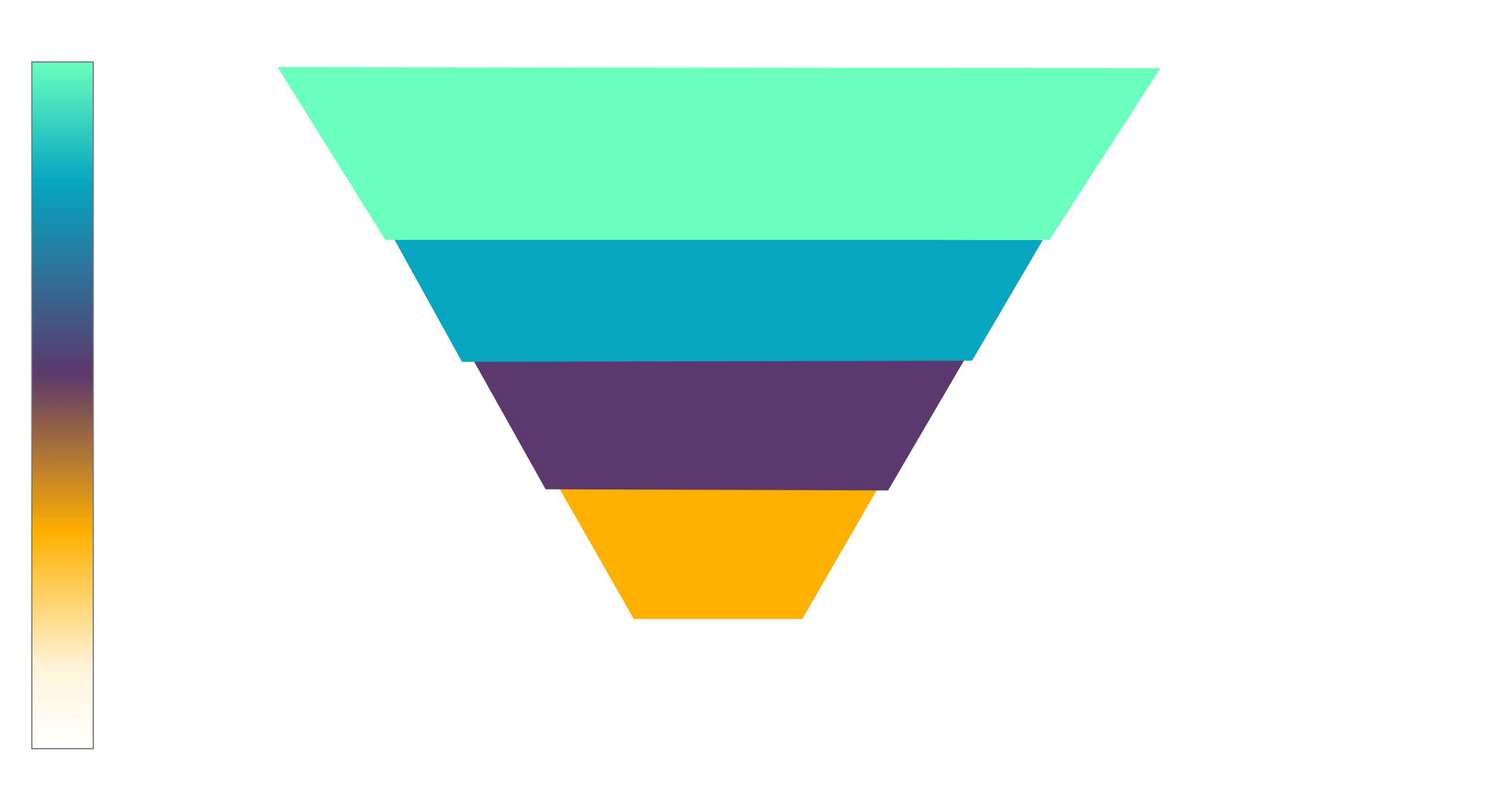
Digitalization has become a powerful tool for us to connect our way of working in safety to our values. In this way, digital is the excuse, what is hidden behind the technology is a new way of working, much more coordinated, agile and focused on helping users to work in a safer and more efficient way:
- The LOTO Digital system has helped us to simplify our planning work, speeding up development times, improving the safety of our employees and enabling traceability analysis
- Our Reporting and Information Management Software allows anyone in our organization, in any location, to activate our Bad News
First philosophy in an agile and practical way
- HSE Bulletin is an internal communication tool for the Graphite Business Unit to increase awareness of HSE learning, improving transparency and knowledge sharing between plants.
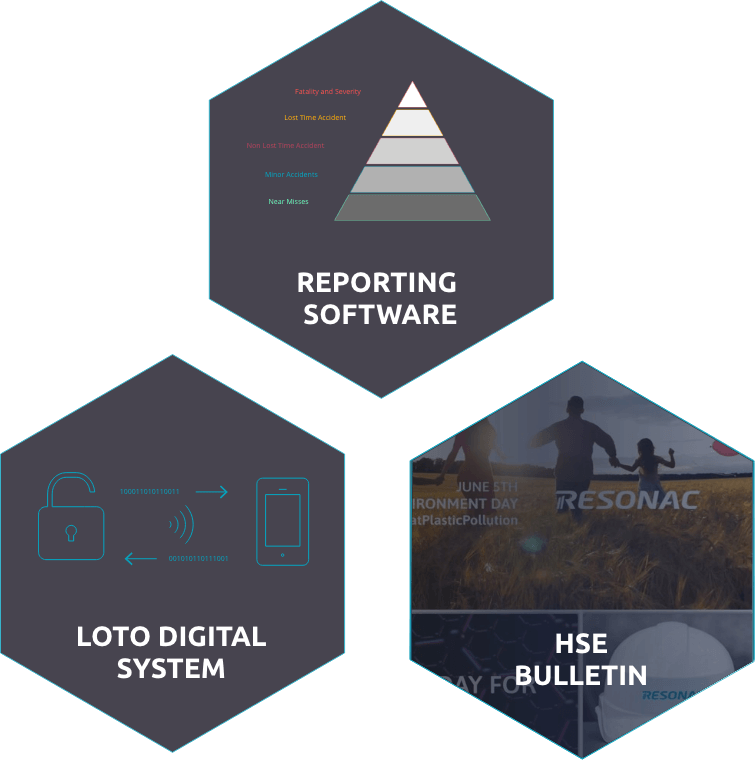
Equality
We are committed to creating a diverse, inclusive and equitable workplace for all our employees. We believe that our differences make us stronger and that everyone should have the opportunity to thrive in our organization. To support this belief, we are implementing a comprehensive Equality program that aims to remove barriers and foster an environment of respect and belonging. This program includes training and development for our employees, specific recruitment and retention initiatives, and regular assessments of our progress toward our Equality goals.
As part of our Employer of Choice program and our commitment to Diversity, Equality, and Inclusion (DEI), we organize a series of events and activities to recognize and highlight the essential role of women in the industry. From thought-provoking panel discussions and inspirational talks to networking sessions and professional development workshops, Women's Week provided an excellent opportunity to reflect on the challenges and achievements of women in the workplace.
We
are
Governance.
We embody governance as a pillar of sustainability. Transparency is at the core of our operations, and we actively engage in third-party assessments and audits to ensure accountability. With a strong focus on ethics and integrity, we have developed a comprehensive compliance program that guides our actions and decision-making processes.
Trans-
parency
At Resonac, we take pride in fostering transparent communication and strong relationships with our customers, stakeholders, and employees. Our commitment to openness is further reinforced by our third-party certifications, including ISO and ECOVADIS, which attest to the rigorous standards we uphold across all our processes. This dedication to transparency and adherence to recognized standards not only strengthens our relationships but also builds trust in our company every day.
- ISO standards are internationally recognized benchmarks that define the best practices for quality,
safety, efficiency, and consistency across various industries. - Ecovadis is a leading sustainability rating platform that assesses and monitors companies’ environmental
and social performance, providing a comprehensive evaluation of their commitment to sustainable and
responsible business practices.
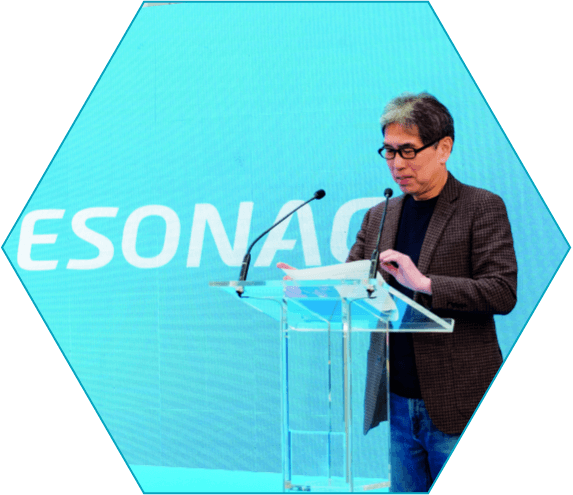
For more information, explore here:
Ethics
and
Integrity
At Resonac, we believe deeply in values and ethics. Our attitude at work is based on four principles: passionate and results-oriented, agile and flexible, open minds and open connections, and strong vision and strong integrity. Our compliance program and our Code of Ethics guide us every day in our workplace, because we firmly believe that ethical behavior is crucial for long-term success.
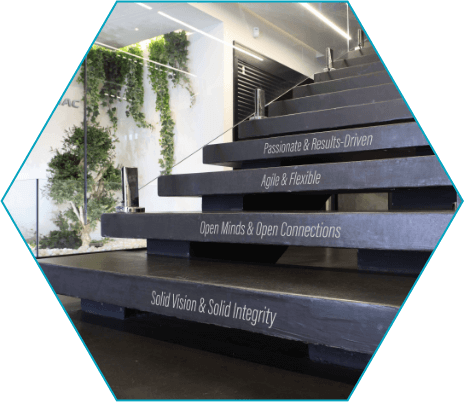
We
are
Sustainable.
We are proud to be a key part of the world’s largest recycling process: the recycling of scrap steel to create new steel.
Our commitment to sustainability is more than a promise; it’s an integral part of our electrode production. From sourcing raw materials like coke and pitch, byproducts of petroleum distillation, to playing a vital role in the global steel recycling process, we embrace sustainability at every step. Our graphite electrodes not only contribute to the circular economy by repurposing waste materials but also serve as key players in steel recycling. As leaders in this essential industry, we take pride in minimizing our environmental footprint. Moreover, our commitment extends to the end of life of our electrodes, ensuring a zero-waste cycle.
Our customers operate so-called Electric Arc Furnaces, where graphite electrodes are the core element of the melting process. Compared to the still dominating method, the creation of steel from iron ore in a Blast Furnace, our products help to save -70% of CO2 emissions*. *Source: Worldsteel COz emission global average intensity
*Source: Worldsteel COz emission global average intensity by production route (tonnes COz per tonne of crude steel cast) (Sustainability Indicators 2023 report - worldsteel.org)
Steel 
industry
with
Resonac.
70%
of CO2 Emissions